Biodiesel
2008/9 Schools Wikipedia Selection. Related subjects: Engineering; Environment
Biodiesel refers to a diesel-equivalent processed fuel consisting of short chain alkyl ( methyl or ethyl) esters, made by transesterification of vegetable oils or animal fats, which can be used (alone, or blended with conventional diesel fuel) in unmodified diesel-engine vehicles.
Biodiesel is distinguished from the straight vegetable oils (SVO) or waste vegetable oils (WVO) used (alone, or blended) as fuels in some diesel vehicles.
On August 31, 1937, G. Chavanne of the University of Brussels (Belgium) was granted a patent for a 'Procedure for the transformation of vegetable oils for their uses as fuels' (fr. 'Procédé de Transformation d’Huiles Végétales en Vue de Leur Utilisation comme Carburants') Belgian Patent 422,877. This patent described the alcoholysis (often referred to as transesterification) of vegetable oils using ethanol (and mentions methanol) in order to separate the fatty acids from the glycerol by replacing the glycerol with short linear alcohols. This appears to be the first account of the production of what is known as 'biodiesel' today.
Biodiesel is biodegradable and non- toxic, and typically produces about 60% less net-lifecycle carbon dioxide emissions, as it is itself produced from atmospheric carbon dioxide via photosynthesis in plants. Its emissions of smog forming hydrocarbon are 65% less, although the Nitrogen Oxide emissions are about 10% greater than those from petroleum-based diesel. Net-lifetime carbon dioxide emissions can actually differ widely between fuels depending upon production methods of the source vegetable oils and processing methods employed in their creation. It is therefore debatable as to the extent that biodiesel reduces total carbon dioxide emissions currently contributing to anthropogenic global warming compared to those from petroleum-based diesel.
Some vehicle manufacturers are positive about the use of biodiesel, citing lower engine wear as one of the fuel's benefits. Biodiesel is a better solvent than standard diesel, as it 'cleans' the engine, removing deposits in the fuel lines. However, this may cause blockages in the fuel injectors if an engine has been previously run on petroleum diesel for years. For this reason, car manufacturers recommend that the fuel filter be changed a few months after switching to biodiesel (the fuel filter, as part of a routine maintenance plan, is generally replaced anyway). Most manufacturers release lists of the cars that will run on 100% biodiesel.
Other vehicle manufacturers remain cautious over use of biodiesel. In the UK many only maintain their engine warranties for use with maximum 5% biodiesel — blended in with 95% conventional diesel — although this position is generally considered to be overly cautious. Scania and Volkswagen are exceptions, allowing most of their engines to operate on 100% biodiesel. Peugeot and Citroën are also exceptions in that they have both recently announced that their PSA HDi engine can run on 30% biodiesel.
The British businessman Richard Branson's Virgin Voyager train, number 220007 Thames Voyager was converted to run on biodiesel, although an adverse effect occurred when it was proven to reduce reliability and to raise costs of maintenance significantly.
Biodiesel can also be used as a heating fuel in domestic and commercial boilers. Existing oil boilers may contain rubber parts and may require conversion to run on biodiesel, but the conversion process is usually relatively simple-- involving the exchanging of rubber parts for synthetic ones due to biodiesel being a strong solvent. One should not burn B100 (pure 100% biodiesel) in an existing home heater without breaking it in, as biodiesel will dissolve coagulated heating oil, which can break off in chunks and cause problems. It is suggested to start by using biodiesel as an additive, and then work your way up to burning biodiesel/petrodiesel mixes of stronger amounts. However, thanks to its strong solvent power, burning biodiesel will increase the efficiency of your home heater.
Biodiesel can be distributed using today's infrastructure, and its use and production are increasing rapidly. Fuel stations are beginning to make biodiesel available to consumers, and a growing number of transport fleets use it as an additive in their fuel. Biodiesel is generally more expensive to purchase than petroleum diesel but this differential may diminish due to economies of scale, the rising cost of petroleum and government tax subsidies.
Description
Biodiesel is a liquid which varies in colour — between golden and dark brown — depending on the production feedstock. It is practically immiscible with water, has a high boiling point and low vapor pressure. Typical methyl ester biodiesel has a flash point of ~ 150 °C (300 °F). Biodiesel has a density of ~ 0.88 g/cm³, less than that of water. Biodiesel has a viscosity similar to petrodiesel, the current industry term for diesel produced from petroleum. It can be used as an additive in formulations of diesel to increase the lubricity of pure Ultra-Low Sulfur Diesel (ULSD) fuel, which is advantageous because it has virtually no sulfur content. Much of the world uses a system known as the "B" factor to state the amount of biodiesel in any fuel mix, in contrast to the "BA" or "E" system used for ethanol mixes. For example, fuel containing 20% biodiesel is labeled B20. Pure biodiesel is referred to as B100.
Biodiesel is a renewable fuel that can be manufactured from algae, vegetable oils, animal fats or recycled restaurant greases; it can be produced locally in most countries. It is safe, biodegradable and reduces air pollutants, such as particulates, carbon monoxide and hydrocarbons. Blends of 20 percent biodiesel with 80 percent petroleum diesel (B20) can generally be used in unmodified diesel engines. Biodiesel can also be used in its pure form (B100), but may require certain engine modifications to avoid maintenance and performance problems.
The volumetric energy density of biodiesel is about 33 MJ/l. This is 9 % lower than regular Number 2 petrodiesel. Variations in biodiesel energy density is more dependent on the feedstock used than the production process. Still these variations are less than for petrodiesel. It has been claimed biodiesel gives better lubricity and more complete combustion thus increasing the engine energy output and partially compensating for the higher energy density of petrodiesel.
Historical background
Transesterification of a vegetable oil was conducted as early as 1853 by scientists E. Duffy and J. Patrick, many years before the first diesel engine became functional. Rudolf Diesel's prime model, a single 10 ft (3 m) iron cylinder with a flywheel at its base, ran on its own power for the first time in Augsburg, Germany, on August 10, 1893. In remembrance of this event, August 10 has been declared "International Biodiesel Day". Diesel later demonstrated his engine and received the Grand Prix (highest prize) at the World Fair in Paris, France in 1900.
This engine stood as an example of Diesel's vision because it was powered by peanut oil — a biofuel, though not biodiesel, since it was not transesterified. He believed that the utilization of biomass fuel was the real future of his engine. In a 1912 speech Diesel said, "the use of vegetable oils for engine fuels may seem insignificant today but such oils may become, in the course of time, as important as petroleum and the coal-tar products of the present time."
During the 1920s, diesel engine manufacturers altered their engines to utilize the lower viscosity of petrodiesel (a fossil fuel), rather than vegetable oil (a biomass fuel). The petroleum industries were able to make inroads in fuel markets because their fuel was much cheaper to produce than the biomass alternatives. The result, for many years, was a near elimination of the biomass fuel production infrastructure. Only recently, have environmental impact concerns and a decreasing price differential made biomass fuels such as biodiesel a growing alternative.
Despite the widespread use of fossil petroleum-derived diesel fuels, interest in vegetable oils as fuels in internal combustion engines is reported in several countries during the 1920's and 1930's and later during World War II. Belgium, France, Italy, the United Kingdom, Portugal, Germany, Brazil, Argentina, Japan and China have been reported to have tested and used vegetable oils as diesel fuels during this time. Some operational problems were reported due to the high viscosity of vegetable oils compared to petroleum diesel fuel, which result in poor atomization of the fuel in the fuel spray and often leads to deposits and coking of the injectors, combustion chamber and valves. Attempts to overcome these problems included heating of the vegetable oil, blending it with petroleum-derived diesel fuel or ethanol, pyrolysis and cracking of the oils.
On August 31, 1937, G. Chavanne of the University of Brussels (Belgium) was granted a patent for a "Procedure for the transformation of vegetable oils for their uses as fuels" (fr. 'Procédé de Transformation d’Huiles Végétales en Vue de Leur Utilisation comme Carburants') Belgian Patent 422,877. This patent described the alcoholysis (often referred to as transesterification) of vegetable oils using methanol and ethanol in order to separate the fatty acids from the glycerol by replacing the glycerol by short linear alcohols. This appears to be the first account of the production of what is known as "biodiesel" today.
More recently, in 1977, Brazilian scientist Expedito Parente produced biodiesel using transesterification with ethanol, and again filed a patent for the same process. This process is classified as biodiesel by international norms, conferring a "standardized identity and quality. No other proposed biofuel has been validated by the motor industry." Currently, Parente's company Tecbio is working with Boeing and NASA to certify bioquerosene (bio-kerosene), another product produced and patented by the Brazilian scientist.
Research into the use of transesterified sunflower oil, and refining it to diesel fuel standards, was initiated in South Africa in 1979. By 1983, the process for producing fuel-quality, engine-tested biodiesel was completed and published internationally. An Austrian company, Gaskoks, obtained the technology from the South African Agricultural Engineers; the company erected the first biodiesel pilot plant in November 1987, and the first industrial-scale plant in April 1989 (with a capacity of 30,000 tons of rapeseed per annum).
Throughout the 1990s, plants were opened in many European countries, including the Czech Republic, Germany and Sweden. France launched local production of biodiesel fuel (referred to as diester) from rapeseed oil, which is mixed into regular diesel fuel at a level of 5%, and into the diesel fuel used by some captive fleets (e.g. public transportation) at a level of 30%. Renault, Peugeot and other manufacturers have certified truck engines for use with up to that level of partial biodiesel; experiments with 50% biodiesel are underway. During the same period, nations in other parts of the world also saw local production of biodiesel starting up: by 1998, the Austrian Biofuels Institute had identified 21 countries with commercial biodiesel projects. 100% Biodiesel is now available at many normal service stations across Europe.
In September 2005 Minnesota became the first U.S. state to mandate that all diesel fuel sold in the state contain part biodiesel, requiring a content of at least 2% biodiesel.
Technical standards
The common international standard for biodiesel is EN 14214.
There are additional national specifications. ASTM D 6751 is the most common standard referenced in the United States and Canada. In Germany, the requirements for biodiesel are fixed in the DIN EN 14214 standard and in the UK the requirements for biodiesel is fixed in the BS EN 14214 standard, although these last two standards are essentially the same as EN 14214 and are just prefixed with the respective national standards institution codes.
There are standards for three different varieties of biodiesel, which are made of different oils:
- RME ( rapeseed methyl ester, according to DIN E 51606)
- PME (vegetable methyl ester, purely vegetable products, according to DIN E 51606)
- FME (fat methyl ester, vegetable and animal products, according to DIN V 51606)
The standards ensure that the following important factors in the fuel production process are satisfied:
- Absence of free fatty acids.
- Low sulfur content.
Basic industrial tests to determine whether the products conform to the standards typically include gas chromatography, a test that verifies only the more important of the variables above. Tests that are more complete are more expensive. Fuel meeting the quality standards is very non-toxic, with a toxicity rating ( LD50) of greater than 50 mL/kg.
Applications
Biodiesel can be used in pure form (B100) or may be blended with petroleum diesel at any concentration in most modern diesel engines. Biodiesel will degrade natural rubber gaskets and hoses in vehicles (mostly found in vehicles manufactured before 1992), although these tend to wear out naturally and most likely will have already been replaced with FKM, which is nonreactive to biodiesel.
Biodiesel has better lubricity than that of today's diesel fuels. During the manufacture of these, to comply with low SO2 engine emission limits set in modern standards, severe hydrotreatment is included. Biodiesel addition reduces wear increasing the life of the fuel injection equipment that relies on the fuel for its lubrication, such as high pressure injection pumps, pump injectors (also called unit injectors) and fuel injectors.
Biodiesel is a better solvent than petrodiesel, and has been known to break down deposits of residue in the fuel lines of vehicles that have previously been run on petrodiesel. As a result, fuel filters and injectors may become clogged with particulates if a quick transition to pure biodiesel is made, as biodiesel “cleans” the engine in the process. Therefore, it is recommended to change the fuel filter within 600–800 miles after first switching to a biodiesel blend.
Use
Pure, non-blended biodiesel can be poured straight into the tank of any diesel vehicle. As with normal diesel, low-temperature biodiesel is sold during winter months to prevent viscosity problems. Some older diesel engines still have natural rubber parts which will be affected by biodiesel, but in practice these rubber parts should have been replaced long ago. Biodiesel is used by millions of car owners in Europe (particularly Germany).
Research sponsored by petroleum producers has found petroleum diesel better for car engines than biodiesel. This has been disputed by independent bodies, including for example the Volkswagen environmental awareness division, who note that biodiesel reduces engine wear. Pure biodiesel produced 'at home' is in use by thousands of drivers who have not experienced failure, however, the fact remains that biodiesel has been widely available at gas stations for less than a decade, and will hence carry more risk than older fuels. Biodiesel sold publicly is held to high standards set by national standards bodies.
Gelling
The temperature at which pure (B100) biodiesel starts to gel varies significantly and depends upon the mix of esters and therefore the feedstock oil used to produce the biodiesel. For example, biodiesel produced from low erucic acid varieties of canola seed (RME) starts to gel at approximately −10 °C (14 °F). Biodiesel produced from tallow tends to gel at around +16 °C (68 °F). As of 2006, there are a very limited number of products that will significantly lower the gel point of straight biodiesel. A number of studies have shown that winter operation is possible with biodiesel blended with other fuel oils including #2 low sulfur diesel fuel and #1 diesel / kerosene. The exact blend depends on the operating environment: successful operations have run using a 65% LS #2, 30% K #1, and 5% bio blend. Other areas have run a 70% Low Sulfur #2, 20% Kerosene #1, and 10% bio blend or an 80% K#1, and 20% biodiesel blend. According to the National Biodiesel Board (NBB), B20 (20% biodiesel, 80% petrodiesel) does not need any treatment in addition to what is already taken with petrodiesel.
Some people modify their vehicles to permit the use of biodiesel without mixing and without the possibility of gelling at low temperatures. This practice is similar to the one used for running straight vegetable oil. They install a second fuel tank (some models of trucks have two tanks already). This second fuel tank is insulated and a heating coil using engine coolant is run through the tank. There is then a temperature sensor installed to notify the driver when the fuel is warm enough to burn, the driver then switches which tank the engine is drawing from.
Contamination by water
Biodiesel may contain small but problematic quantities of water. Although it is hydrophobic (non-miscible with water molecules), it is said to be, at the same time, hygroscopic to the point of attracting water molecules from atmospheric moisture; in addition, there may be water that is residual to processing or resulting from storage tank condensation. The presence of water is a problem because:
- Water reduces the heat of combustion of the bulk fuel. This means more smoke, harder starting, less power.
- Water causes corrosion of vital fuel system components: fuel pumps, injector pumps, fuel lines, etc.
- Water & microbes cause the paper element filters in the system to fail ( rot), which in turn results in premature failure of the fuel pump due to ingestion of large particles.
- Water freezes to form ice crystals near 0 °C (32 °F). These crystals provide sites for nucleation and accelerate the gelling of the residual fuel.
- Water accelerates the growth of microbe colonies, which can plug up a fuel system. Biodiesel users who have heated fuel tanks therefore face a year-round microbe problem.
Previously, the amount of water contaminating biodiesel has been difficult to measure by taking samples, since water and oil separate. However, it is now possible to measure the water content using water in oil sensors.
Heating applications
Biodiesel can also be used as a heating fuel in domestic and commercial boilers. A technical research paper describes laboratory research and field trials project using pure biodiesel and biodiesel blends as a heating fuel in oil fired boilers. During the Biodiesel Expo 2006 in the UK, Andrew J. Robertson presented his biodiesel heating oil research from his technical paper and suggested that B20 biodiesel could reduce UK household CO2 emissions by 1.5 million tonnes per year and would only require around 330,000 hectares of arable land for the required biodiesel for the UK heating oil sector. The paper also suggests that existing oil boilers can easily and cheaply be converted to biodiesel if B20 biodiesel is used.
Availability and prices
Global biodiesel production reached 3.8 million tons in 2005. Approximately 85% of biodiesel production came from the European Union.
Retail, at the pump, prices including Federal and state motor taxes, of B2/B5 are lower than petroleum diesel by about 12 cents, and B20 blends are the same as petrodiesel.
Production
Chemically, transesterified biodiesel comprises a mix of mono- alkyl esters of long chain fatty acids. The most common form uses methanol to produce methyl esters as it is the cheapest alcohol available, though ethanol can be used to produce an ethyl ester biodiesel and higher alcohols such as isopropanol and butanol have also been used. Using alcohols of higher molecular weights improves the cold flow properties of the resulting ester, at the cost of a less efficient transesterification reaction. A lipid transesterification production process is used to convert the base oil to the desired esters. Any Free fatty acids (FFAs) in the base oil are either converted to soap and removed from the process, or they are esterified (yielding more biodiesel) using an acidic catalyst. After this processing, unlike straight vegetable oil, biodiesel has combustion properties very similar to those of petroleum diesel, and can replace it in most current uses.
A byproduct of the transesterification process is the production of glycerol. For every 1 tonne of biodiesel that is manufactured, 100 kg of glycerol are produced. Originally, there was a valuable market for the glycerol, which assisted the economics of the process as a whole. However, with the increase in global biodiesel production, the market price for this crude glycerol (containing 20% water and catalyst residues) has crashed. Research is being conducted globally to use this glycerol as a chemical building block. One initiative in the UK is The Glycerol Challenge.
Usually this crude glycerol has to be purified, typically by performing vacuum distillation. This is rather energy intensive. The refined glycerol (98%+ purity) can then be utilised directly, or converted into other products. The following announcements were made in 2007: A joint venture of Ashland Inc. and Cargill announced plans to make propylene glycol in Europe from glycerol and Dow Chemical announced similar plans for North America. Dow also plans to build a plant in China to make epichlorhydrin from glycerol. Epichlorhydrin is a raw material for epoxy resins.
Biodiesel feedstock
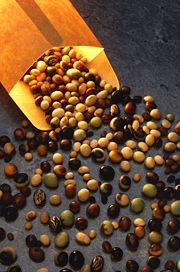
Plant oils | |
---|---|
Sunflowerseed oil | |
Types | |
Vegetable fats | (list) |
Essential oil | ( list) |
Macerated | ( list) |
Uses | |
Drying oil - Oil paint | |
Cooking oil | |
Fuel - Biodiesel | |
Aromatherapy | |
Components | |
Saturated fat | |
Monounsaturated fat | |
Polyunsaturated fat | |
Trans fat |
A variety of oils can be used to produce biodiesel. These include:
- Virgin oil feedstock; rapeseed and soybean oils are most commonly used, soybean oil alone accounting for about ninety percent of all fuel stocks; It also can be obtained from field pennycress and Jatropha other crops such as mustard, flax, sunflower, palm oil, hemp, and even algae show promise (see List of vegetable oils for a more complete list);
- Waste vegetable oil (WVO);
- Animal fats including tallow, lard, yellow grease, chicken fat, and the by-products of the production of Omega-3 fatty acids from fish oil.
- Sewage. A company in New Zealand has successfully developed a system for using sewage waste as a substrate for algae and then producing bio-diesel.
Worldwide production of vegetable oil and animal fat is not yet sufficient to replace liquid fossil fuel use. Furthermore, some environmental groups object to the vast amount of farming and the resulting over-fertilization, pesticide use, and land use conversion that they say would be needed to produce the additional vegetable oil.
Many advocates suggest that waste vegetable oil is the best source of oil to produce biodiesel. However, the available supply is drastically less than the amount of petroleum-based fuel that is burned for transportation and home heating in the world. It is important to note that one unit of waste oil is not equivalent to one unit of biodiesel.
Although it is economically profitable to use WVO to produce biodiesel, it is even more profitable to convert WVO into other products such as soap. Therefore, most WVO that is not dumped into landfills is used for these other purposes. Animal fats are similarly limited in supply, and it would not be efficient to raise animals simply for their fat. However, producing biodiesel with animal fat that would have otherwise been discarded could replace a small percentage of petroleum diesel usage. Currently, a 5-million dollar plant is being built, with the intent of producing biodiesel from some of the estimated 1.05 million tonnes (2.3 billion pounds) of chicken fat produced annually the local Tyson poultry plant, though insiders estimate a potential production of 1.1 billion litres (300 million gallons) of fuel from the chicken fat feedstock.
The estimated transportation diesel fuel and home heating oil used in the United States is about 190 billion litres (50 billion US gallons) according to the Energy Information Administration, US Department of Energy - . Waste vegetable oil and animal fats would not be enough to meet this demand. In the United States, estimated production of vegetable oil for all uses is about 11 million tonnes (24 billion pounds) or 11 billion litres (3 billion US gallons), and estimated production of animal fat is 5.3 million tonnes (12 billion pounds).
Biodiesel feedstock plants utilize photosynthesis to convert solar energy into chemical energy. The stored chemical energy is released when it is burned, therefore plants can offer a sustainable oil source for biodiesel production. Most of the carbon dioxide emitted when burning biodiesel is simply recycling that which was absorbed during plant growth, so the net production of greenhouse gases is small.
Feedstock yield efficiency per acre affects the feasibility of ramping up production to the huge industrial levels required to power a significant percentage of national or world vehicles. The highest yield feedstock for biodiesel is algae, which can produce 250 times the amount of oil per acre as soybeans.
Yields of common crops
Crop | kg oil/ ha | litres oil/ ha | lbs oil/ acre | US gal/ acre |
---|---|---|---|---|
corn (maize) | 145 | 172 | 129 | 18 |
cashew nut | 148 | 176 | 132 | 19 |
oats | 183 | 217 | 163 | 23 |
lupine | 195 | 232 | 175 | 25 |
kenaf | 230 | 273 | 205 | 29 |
calendula | 256 | 305 | 229 | 33 |
cotton | 273 | 325 | 244 | 35 |
hemp | 305 | 363 | 272 | 39 |
soybean | 375 | 446 | 335 | 48 |
coffee | 386 | 459 | 345 | 49 |
linseed (flax) | 402 | 478 | 359 | 51 |
hazelnuts | 405 | 482 | 362 | 51 |
euphorbia | 440 | 524 | 393 | 56 |
pumpkin seed | 449 | 534 | 401 | 57 |
coriander | 450 | 536 | 402 | 57 |
mustard seed | 481 | 572 | 430 | 61 |
camelina | 490 | 583 | 438 | 62 |
sesame | 585 | 696 | 522 | 74 |
safflower | 655 | 779 | 585 | 83 |
rice | 696 | 828 | 622 | 88 |
tung oil tree | 790 | 940 | 705 | 100 |
sunflowers | 800 | 952 | 714 | 102 |
cocoa (cacao) | 863 | 1,026 | 771 | 110 |
peanuts | 890 | 1,059 | 795 | 113 |
opium poppy | 978 | 1,163 | 873 | 124 |
rapeseed ( Canola) | 1,000 | 1,190 | 893 | 127 |
olives | 1,019 | 1,212 | 910 | 129 |
castor beans | 1,188 | 1,413 | 1,061 | 151 |
pecan nuts | 1,505 | 1,791 | 1,344 | 191 |
jojoba | 1,528 | 1,818 | 1,365 | 194 |
jatropha | 1,590 | 1,892 | 1,420 | 202 |
macadamia nuts | 1,887 | 2,246 | 1,685 | 240 |
Brazil nuts | 2,010 | 2,392 | 1,795 | 255 |
avocado | 2,217 | 2,638 | 1,980 | 282 |
coconut | 2,260 | 2,689 | 2,018 | 287 |
oil palm | 5,000 | 5,950 | 4,465 | 635 |
Chinese tallow | 5,500 | 6,545 | 4,912 | 699 |
Algae (actual yield)* | 6,894 | 7,660 | 6,151 | 819 |
Algae (theoretical yield)** | 39,916 | 47,500 | 35,613 | 5,000 |
* Actual biomass algae yields from field trials conducted during the NREL's aquatic species program, converted using the actual oil content of the algae species grown in the specific trials. ** Algae yields are projected based on the sustainable average biomass yields of the NREL's aquatic species program, and an assumed oil content of 60%. Actual oil content was much less.
- Note: Chinese tallow ( Triadica Sebifera, or Sapium sebiferum) is also known as the "Popcorn Tree" or Florida Aspen.
Source: Chinese tallow data, Mississippi State University
Source: Used with permission from the The Global Petroleum Club
Typical oil extraction from 100 kg. of oil seeds
Crop | Oil/100kg. |
---|---|
Castor Seed | 50 kg |
Copra | 62 kg |
Cotton Seed | 13 kg |
Groundnut Kernel | 42 kg |
Mustard | 35 kg |
Palm Kernel | 36 kg |
Palm Fruit | 20 kg |
Rapeseed | 37 kg |
Sesame | 50 kg |
Soybean | 14 kg |
Sunflower | 32 kg |
Source: Petroleum Club (with permission)
The energy content of biodiesel is about 90 percent that of petroleum diesel.
Efficiency and economic arguments
According to a study written by Drs. Van Dyne and Raymer for the Tennessee Valley Authority, the average US farm consumes fuel at the rate of 82 litres per hectare (8.75 US gallons per acre) of land to produce one crop. However, average crops of rapeseed produce oil at an average rate of 1,029 L/ha (110 US gal/acre), and high-yield rapeseed fields produce about 1,356 L/ha (145 US gal/acre). The ratio of input to output in these cases is roughly 1:12.5 and 1:16.5. Photosynthesis is known to have an efficiency rate of about 3-6% of total solar radiation and if the entire mass of a crop is utilized for energy production, the overall efficiency of this chain is known to be about 1%. This does not compare favorably to solar cells combined with an electric drive train, however biodiesel out-competes solar cells in cost and ease of deployment as solar cells still cost approximately US$1,000 per square meter. However, these statistics by themselves are not enough to show whether such a change makes economic sense. Additional factors must be taken into account, such as: the fuel equivalent of the energy required for processing, the yield of fuel from raw oil, the return on cultivating food, the effect biodiesel will have of food prices and the relative cost of biodiesel versus petrodiesel. A 1998 joint study by the U.S. Department of Energy (DOE) and the U.S. Department of Agriculture (USDA) traced many of the various costs involved in the production of biodiesel and found that overall, it yields 3.2 units of fuel product energy for every unit of fossil fuel energy consumed. That measure is referred to as the energy yield. A comparison to petroleum diesel, petroleum gasoline and bioethanol using the USDA numbers can be found at the Minnesota Department of Agriculture website In the comparison petroleum diesel fuel is found to have a 0.843 energy yield, along with 0.805 for petroleum gasoline, and 1.34 for bioethanol. The 1998 study used soybean oil primarily as the base oil to calculate the energy yields. Furthermore, due to the higher energy density of biodiesel, combined with the higher efficiency of the diesel engine, a unit of biodiesel produces the effective energy of 2.25 units of ethanol. Also, higher oil yielding crops could increase the energy yield of biodiesel. However not all oils retain the same heat capacities.
The debate over the energy balance of biodiesel is ongoing. Generally is 2.5. Transitioning fully to biofuels could require immense tracts of land if traditional food crops are used (although non food crops can be utilized). The problem would be especially severe for nations with large economies, since energy consumption scales with economic output. If using only traditional food plants, most such nations do not have sufficient arable land to produce biofuel for the nation's vehicles. Nations with smaller economies (hence less energy consumption) and more arable land may be in better situations, although many regions cannot afford to divert land away from food production. For third world countries, biodiesel sources that use marginal land could make more sense, e.g. honge oil nuts grown along roads or jatropha grown along rail lines. More recent studies using a species of algae with up to 50% oil content have concluded that only 28,000 km² or 0.3% of the land area of the US could be utilized to produce enough biodiesel to replace all transportation fuel the country currently utilizes. Furthermore, otherwise unused desert land (which receives high solar radiation) could be most effective for growing the algae, and the algae could utilize farm waste and excess CO2 from factories to help speed the growth of the algae. In tropical regions, such as Malaysia and Indonesia, oil palm is being planted at a rapid pace to supply growing biodiesel demand in Europe and other markets. It has been estimated in Germany that palm oil biodiesel has less than 1/3 the production costs of rapeseed biodiesel. The direct source of the energy content of biodiesel is solar energy captured by plants during photosynthesis. The website biodiesel.co.uk discusses the positive energy balance of biodiesel:
- When straw was left in the field, biodiesel production was strongly energy positive, yielding 1 GJ biodiesel for every 0.561 GJ of energy input (a yield/cost ratio of 1.78).
- When straw was burned as fuel and oilseed rapemeal was used as a fertilizer, the yield/cost ratio for biodiesel production was even better (3.71). In other words, for every unit of energy input to produce biodiesel, the output was 3.71 units (the difference of 2.71 units would be from solar energy).
Biodiesel is becoming of interest to companies interested in commercial scale production as well as the more usual home brew biodiesel user and the user of straight vegetable oil or waste vegetable oil in diesel engines. Homemade biodiesel processors are many and varied. The success of biodiesel homebrewing, and micro-economy-of-scale operations, continues to shatter the conventional business myth that large economy-of-scale operations are the most efficient and profitable. It is becoming increasingly apparent that small-scale, localized, low-impact energy keeps more resources and revenue within communities, reduces damage to the environment, and requires less waste management.
Environmental benefits
Environmental benefits in comparison to petroleum based fuels include:
- "At the tailpipe, biodiesel emits 4.7% more CO2 than petroleum diesel". However, if "biomass carbon [is] accounted for separately from fossil-derived carbon", one can conclude that biodiesel reduces emissions of carbon monoxide (CO) by approximately 50% and carbon dioxide by 78% on a net lifecycle basis because the carbon in biodiesel emissions is recycled from carbon that was in the atmosphere, rather than the carbon introduced from petroleum that was sequestered in the earth's crust.
- Biodiesel contains fewer aromatic hydrocarbons: benzofluoranthene: 56% reduction; Benzopyrenes: 71% reduction.
- Biodiesel can reduce by as much as 20% the direct (tailpipe) emission of particulates, small particles of solid combustion products, on vehicles with particulate filters, compared with low-sulfur (<50 ppm) diesel. Particulate emissions as the result of production are reduced by around 50%, compared with fossil-sourced diesel. (Beer et al, 2004).
- Biodiesel has a higher cetane rating than petrodiesel, which can improve performance and clean up emissions compared to crude petro-diesel (with cetane lower than 40).
- Biodiesel is considered readily biodegradable under ideal conditions and non-toxic. A University of Idaho study compared biodegradation rates of biodiesel, neat vegetable oils, biodiesel and petroleum diesel blends, and neat 2-D diesel fuel. Using low concentrations of the product to be degraded (10 ppm) in nutrient and sewage sludge amended solutions, they demonstrated that biodiesel degraded at the same rate as a dextrose control and 5 times as quickly as petroleum diesel over a period of 28 days, and that biodiesel blends doubled the rate of petroleum diesel degradation through co-metabolism . The same study examined soil degradation using 10 000 ppm of biodiesel and petroleum diesel, and found biodiesel degraded at twice the rate of petroleum diesel in soil. In all cases, it was determined biodiesel also degraded more completely than petroleum diesel, which produced poorly degradable undetermined intermediates. Toxicity studies for the same project demonstrated no mortalities and few toxic effects on rats and rabbits with up to 5000 mg/kg of biodiesel. Petroleum diesel showed no mortalities at the same concentration either, however toxic effects such as hair loss and urinary discolouring were noted with concentrations of >2000 mg/l in rabbits.
- In the United States, biodiesel is the only alternative fuel to have successfully completed the Health Effects Testing requirements (Tier I and Tier II) of the Clean Air Act (1990).
- Since biodiesel is more often used in a blend with petroleum diesel, there are fewer formal studies about the effects on pure biodiesel in unmodified engines and vehicles in day-to-day use. Fuel meeting the standards and engine parts that can withstand the greater solvent properties of biodiesel is expected to--and in reported cases does--run without any additional problems than the use of petroleum diesel.
- The flash point of biodiesel (>150 °C) is significantly higher than that of petroleum diesel (64 °C) or gasoline (−45 °C). The gel point of biodiesel varies depending on the proportion of different types of esters contained. However, most biodiesel, including that made from soybean oil, has a somewhat higher gel and cloud point than petroleum diesel. In practice this often requires the heating of storage tanks, especially in cooler climates.
- Pure biodiesel (B100) can be used in any petroleum diesel engine, though it is more commonly used in lower concentrations. Some areas have mandated ultra-low sulfur petrodiesel, which reduces the natural viscosity and lubricity of the fuel due to the removal of sulfur and certain other materials. Additives are required to make ULSD properly flow in engines, making biodiesel one popular alternative. Ranges as low as 2% (B2) have been shown to restore lubricity. Many municipalities have started using 5% biodiesel (B5) in snow-removal equipment and other systems.
Environmental concerns
The locations where oil-producing plants are grown is of increasing concern to some environmentalists, one of the prime worries being that countries may clear cut large areas of tropical forest in order to grow such oil rich crops such as oil palm. In the Philippines and Indonesia such forest clearing is already underway for the production of palm oil for food. Loss of habitat on such a scale could endanger numerous species of plants and animals. A particular concern which has received considerable attention is the threat to the already-shrinking populations of orangutans on the Indonesian islands of Borneo and Sumatra, which face possible extinction.
Biodiesel and feedstock oils produced in Asia, South America and Africa are currently less expensive than those produced in Europe and North America suggesting that imports to these wealthier nations are likely to increase in future. Like all petroleum based fuels, biodiesel also requires a significant investment of energy before it arrives at petrol pumps, thus fair comparisons among fuels require full lifecycle analyses for each fuel type. The US EPA currently estimates that the use of biodiesel represents a 67% reduction in greenhouse gas emissions in comparison with petroleum based fuels. If deforestation, and monoculture farming techniques were used to grow biofuel crops, biodiesel is predicted to become a serious threat to the environment. These problems could be exacerbated as biodiesel becomes more popular unless stringent laws are introduced and enforced to control biodiesel production. Non-food energy crops and lipid rich algaes with vastly greater oil yields may also replace low-yield annual food crops such as soybeans, skirting the deforestation risk associated with widespread uptake of biodiesel.
As non-food crops also facilitate the use of degraded lands, wastewater, processed sewage, and other waste streams, the benefits of such crops go well beyond their greater yields. Moreover, select non-food crops such as jatropha and castorbean can be grown in polycultures, in non-till agricultural applications, and they scale well from the standpoint of production, storage, and processing. As such, these crops have considerable promise for small-scale farmers throughout tropical and temperate latitudes, providing a cash crop option which can also displace local demand for imported petroleum.
If burned without additives, Biodiesel (B100) is estimated to produce about 10% more nitrogen oxide NOx tailpipe-emissions than petrodiesel. As biodiesel has a low sulfur content, NOx emissions can be reduced through the use of catalytic converters to less than the NOx emissions from conventional diesel engines. Moreover, as a transportation fuel, biodiesel is in its infancy in terms of additives which are capable of improving energy density, resistance to gelling, and NOxemissions. Debate continues over NOx, particulates, smog, and greenhouse gas emissions from biodiesel and all other new transportation fuels, biofuels in particular. Ultimately, greater clarity on the fundamental distinctions between smog and other local pollution issues vs. greenhouse gas emissions will be essential for both well founded public policy as well as well informend consumer choices. In February 2006 a Navy biodiesel expert claimed NOx emissions in practice were actually lower than baseline. Further research is needed.
Recent advances in the use of cerium oxide, however, hold the potential to nearly eliminate NOx emissions from both petrodiesel and biodiesel, and diesel fuel additives based on cerium oxide can improve fuel consumption by 11% in unmodified diesel engines.
Current research
There is ongoing research into finding more suitable crops and improving oil yield. Using the current yields, vast amounts of land and fresh water would be needed to produce enough oil to completely replace fossil fuel usage. It would require twice the land area of the US to be devoted to soybean production, or two-thirds to be devoted to rapeseed production, to meet current US heating and transportation needs.
Specially bred mustard varieties can produce reasonably high oil yields, and have the added benefit that the meal leftover after the oil has been pressed out can act as an effective and biodegradable pesticide.
Algaculture
From 1978 to 1996, the U.S. National Renewable Energy Laboratory experimented with using algae as a biodiesel source in the " Aquatic Species Program". A self-published article by Michael Briggs, at the UNH Biodiesel Group, offers estimates for the realistic replacement of all vehicular fuel with biodiesel by utilizing algae that have a natural oil content greater than 50%, which Briggs suggests can be grown on algae ponds at wastewater treatment plants. This oil-rich algae can then be extracted from the system and processed into biodiesel, with the dried remainder further reprocessed to create ethanol.
The production of algae to harvest oil for biodiesel has not yet been undertaken on a commercial scale, but feasibility studies have been conducted to arrive at the above yield estimate. In addition to its projected high yield, algaculture — unlike crop-based biofuels — does not entail a decrease in food production, since it requires neither farmland nor fresh water. Some companies are pursuing algae bio-reactors for various purposes, including biodiesel production.
On May 11, 2006 the Aquaflow Bionomic Corporation in Marlborough, New Zealand announced that it had produced its first sample of bio-diesel fuel made from algae found in sewage ponds. Unlike previous attempts, the algae was naturally grown in pond discharge from the Marlborough District Council's sewage treatment works.